Then I fitted the “menu†push button for the instrument.
As its convenient to select various functions as you are riding I chose to mount this switch on the left hand handlebar switch cluster. Some people choose to wire the flasher switch to provide this function, but instead I chose simply to drill and fit the switch on the front (of bike) lower side of the switch casting.
Finally it’s time to make the mount for the instrument. The mount is going to sit the meter on top of the aluminium Harley headlight mount - I chose to mount it there and not on the top yoke as the casting is rubber mounted.
The instrument has three M4 tapped holes in the back, the cover I purchased is like a cup that goes over the back of the instrument and around its sides to make it look neat- it comes with a choice of screws that either hold the cover on (short) or can also hold an additional bracket (long). The cable for the instrument sticks out the middle of the rear face.
There are a few options to mount the instrument, a simple bent metal bracket to the rear, or a ring style thin bracket that slips between the cover and the front rim of the dial.
I didn’t like either of these as the wire was left exposed and didn’t look neat- and to get the bend in the wire was going to stick the instrument up high again.
Obviously the instrument has to point at the driver so it needs to be angled differently from the rest of the bits on the headstock. The angle is quite important for these instruments as the idiot lights are high brightness LEDs and have quite a narrow angle of their beam- “on axis†they are very bright but “off axis†they are very dim. The instrument has to point at your face.
After several hours of thinking I realised it was going to need a machined lump of alloy that matched the back of the instrument and matched the top of the headlight mount- but all machined at an angle. The instrument would then look like part of the headlight mount as there would be no gaps and the wire will be hidden. I measured the critical angles (using a little digital spirit level) and sketched something out, then I sorted out the top fixings and opened up the hole in the headlight mount so the cable connectors slipped thru.
Finally it was time to rummage around the scrap bin and start machining on my trusted Chinese lathe which after 25 years I actually like now.
I did three main upgrades to the lathe to make it good.
1: swap the motor for a 3 phase motor with speed and direction control. That makes it quiet and easy to manage the speed.
2: I added digital readouts to the slides- this makes the inaccuracy of the lead screws irrelevant.
3: I added sops at the ends of the gib strips- this is a particularly poor aspect of these machines that makes most people fed up with them – the gib strips are not located with a dowel and so move ever-so-slightly causing them to jam. To prevent this people run the gibs loose and so everything gets sloppy. A little plate at each end of the castings with grub screws to prevent movement and the slideways are tight but free running. It’s worth the work- I’ve seen all of these mods done to British/US lathes too.
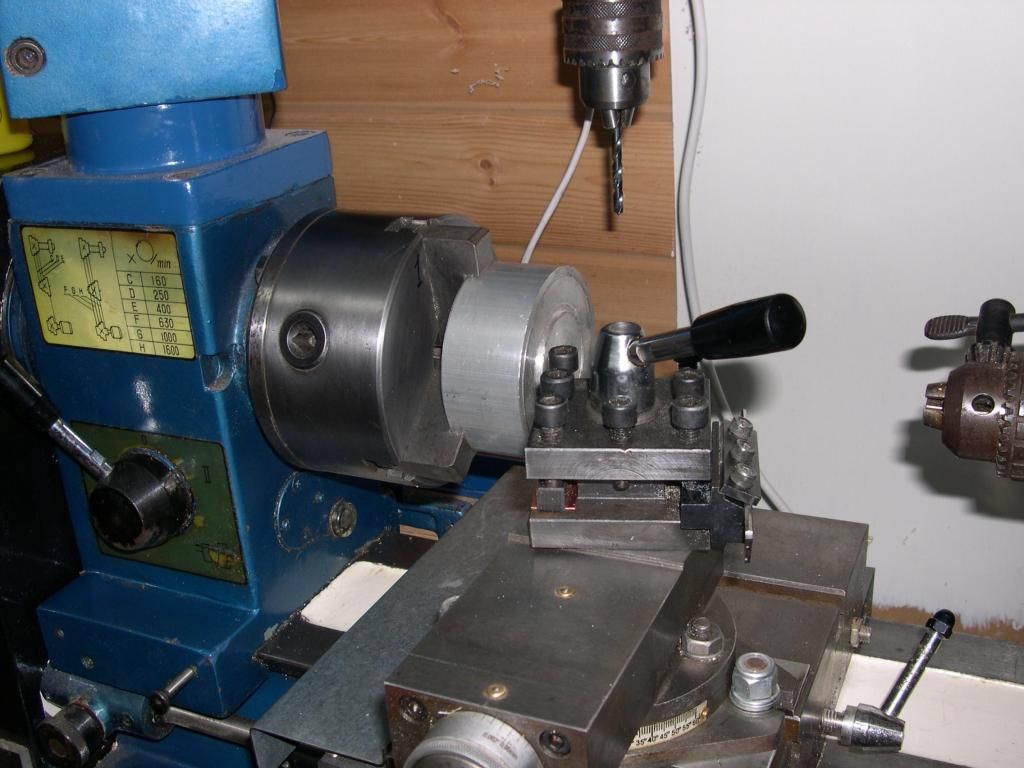
z650/1400 bonneville hybrid.