
Hello Guest User,
Please feel free to have a look around the forum but be aware that as an unregistered guest you can't see all of it and you can't post.
To access these 'Registered Users Only' areas simply register and login.
Please feel free to have a look around the forum but be aware that as an unregistered guest you can't see all of it and you can't post.
To access these 'Registered Users Only' areas simply register and login.
My Ultimate Zed
Moderators: KeithZ1R, chrisu, paul doran, Taffus
- Zomerset Zed
- 100Club
- Posts: 129
- Joined: 30th May 2014
- Location: Somerset
- Zomerset Zed
- 100Club
- Posts: 129
- Joined: 30th May 2014
- Location: Somerset
A bit of progress
Haven't been able to get too much done on the Zed recently as work getting in the way!
But i have done the following:
Cut and shaped 25mm tubes to brace the frame:
These took quite a bit of work with the die grinder to get a nice neat fit and a half decent weld prep. I then tacked them in place in the frame:
[/img]
Also got me some R6 USD forks and some TEC piggy back shocks to fit:
Amazingly it looks like i do not have to modify the steering stem to fit, just fit some new taper roller bearings and get a new top yoke designed and machined to fit. I may have to look at extending the forks a little bit hopefully all internally.
I will be fabricating new top shock mounts to move them forward by about 90mm and designing and making some new ally mounts to weld to the swingarm to get the look and geometry correct.
This will bring the distance from the swingarm pivot to the lower shock mount centres equal to the distance between the swingarm pivot and the top shock mount centres. This will ensure a slight rising rate to the wheel travel/spring force relationship.
Before i cut any metal i need to get the ground clearance right so its not too low or high at the rear. Anyone know what standard ground clearance is between the bottom of the frame rails and the floor?
But i have done the following:
Cut and shaped 25mm tubes to brace the frame:
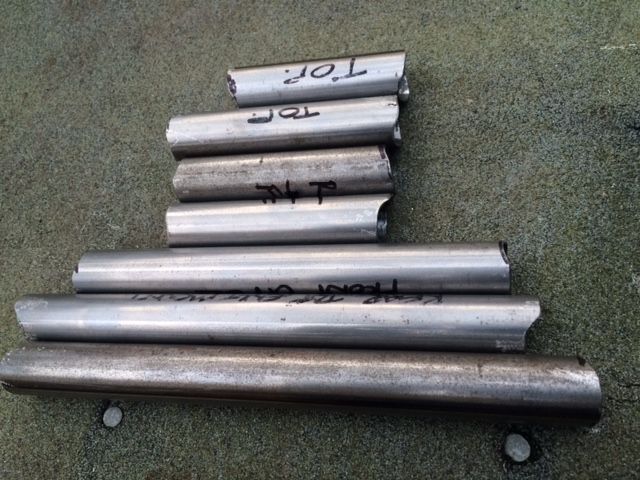
These took quite a bit of work with the die grinder to get a nice neat fit and a half decent weld prep. I then tacked them in place in the frame:
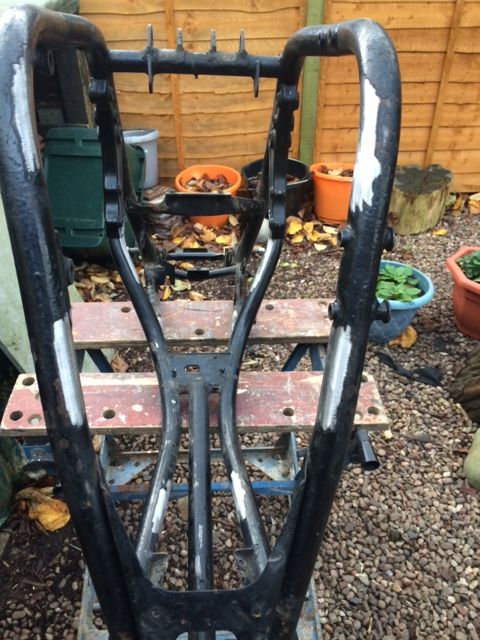
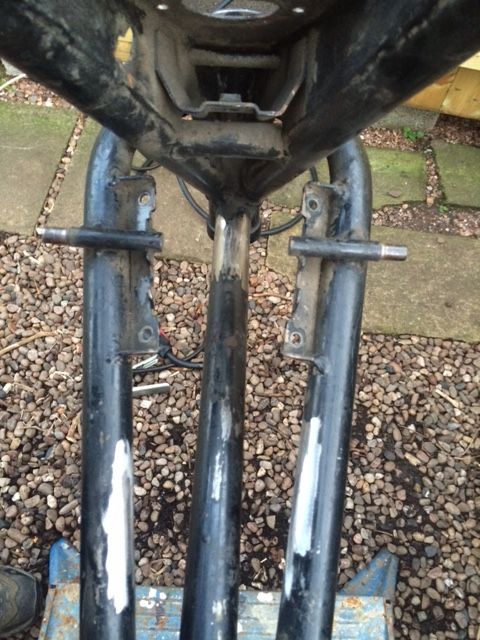
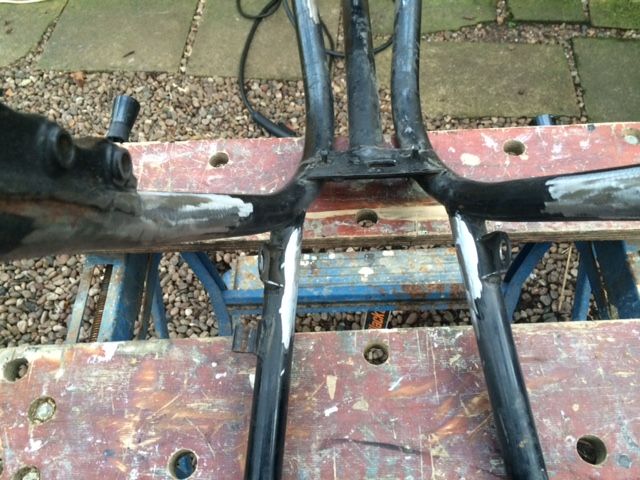
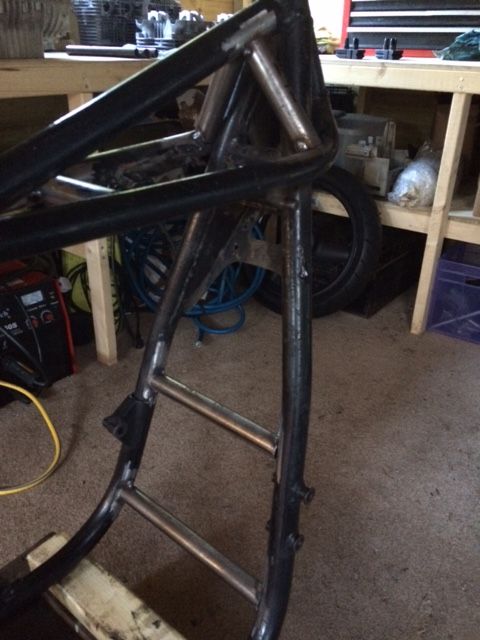
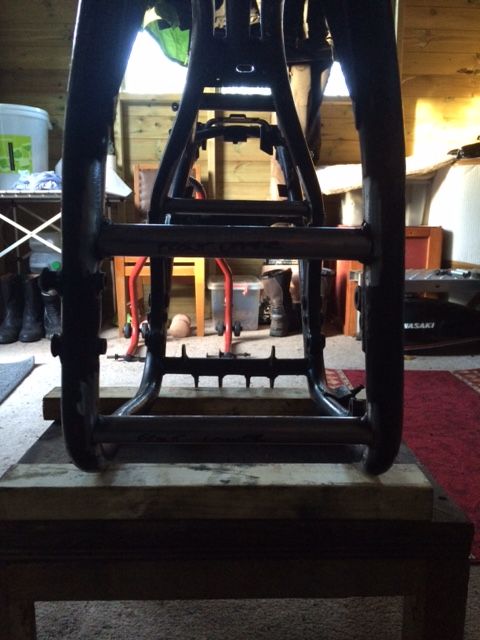
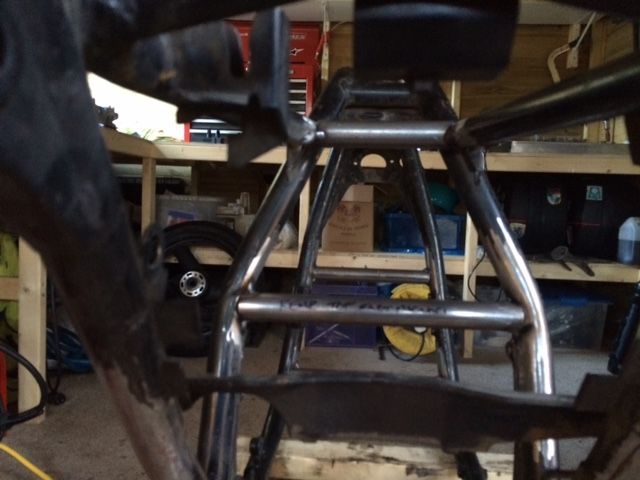
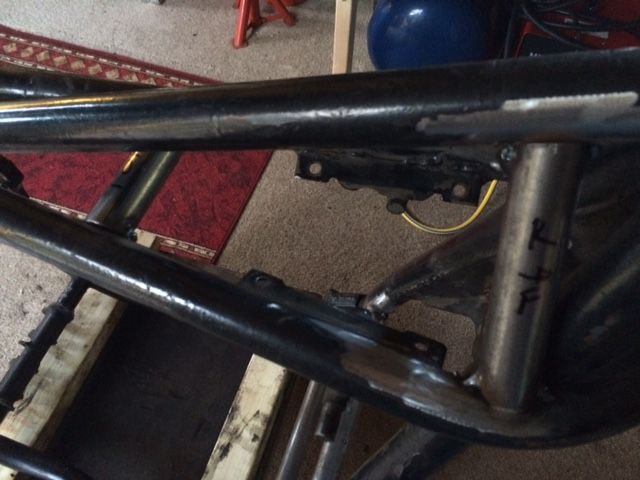
Also got me some R6 USD forks and some TEC piggy back shocks to fit:
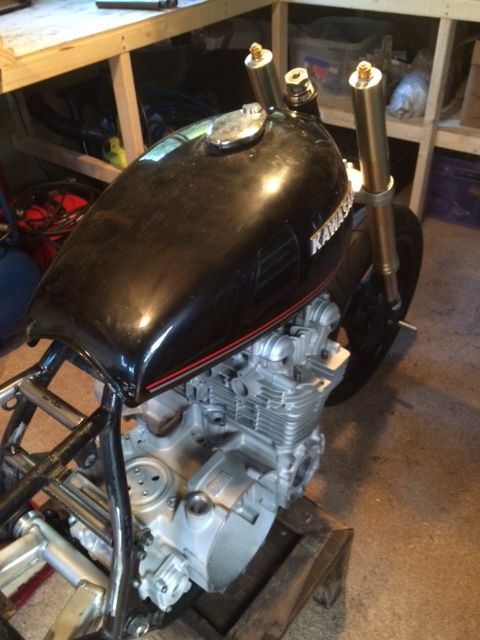
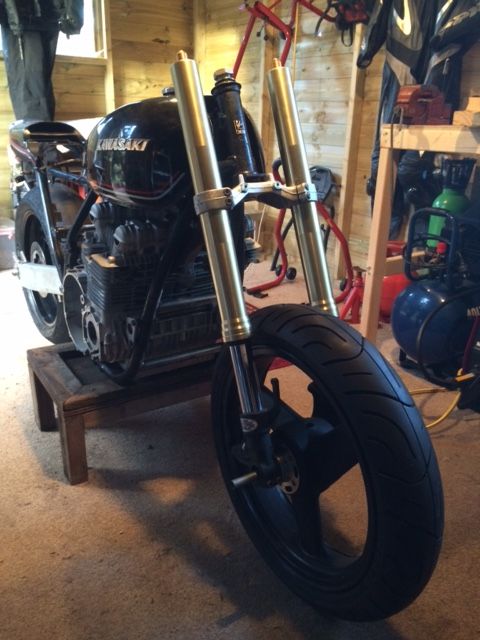
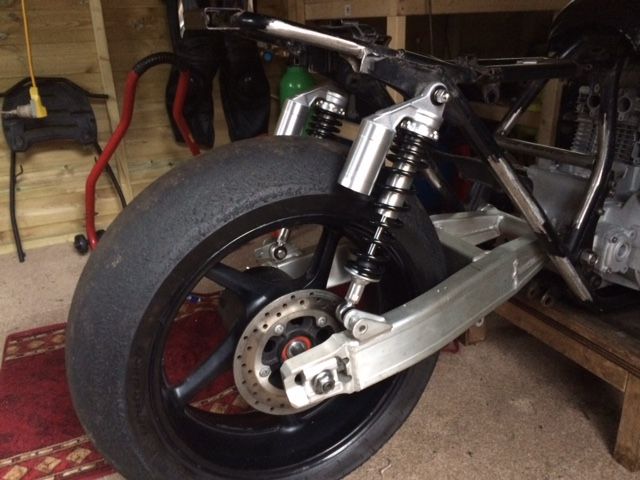
Amazingly it looks like i do not have to modify the steering stem to fit, just fit some new taper roller bearings and get a new top yoke designed and machined to fit. I may have to look at extending the forks a little bit hopefully all internally.
I will be fabricating new top shock mounts to move them forward by about 90mm and designing and making some new ally mounts to weld to the swingarm to get the look and geometry correct.
This will bring the distance from the swingarm pivot to the lower shock mount centres equal to the distance between the swingarm pivot and the top shock mount centres. This will ensure a slight rising rate to the wheel travel/spring force relationship.
Before i cut any metal i need to get the ground clearance right so its not too low or high at the rear. Anyone know what standard ground clearance is between the bottom of the frame rails and the floor?
-
- 100Club
- Posts: 389
- Joined: 28th Mar 2013
- Location: Swindon Wiltshire
This looks like it will be a good Z !!
I just measured my uni-trak bottom frame rails directly under the clutch cover ,bike bolt up-right and it is approx 230 - 240 mm and that is from the bottom of frame rail to level flat floor , but i am sure someone on here will give you the Z measurments ,but i cant see it being loads different ?
I hope that helps you a bit ,,,,,,,,, Andy
I just measured my uni-trak bottom frame rails directly under the clutch cover ,bike bolt up-right and it is approx 230 - 240 mm and that is from the bottom of frame rail to level flat floor , but i am sure someone on here will give you the Z measurments ,but i cant see it being loads different ?
I hope that helps you a bit ,,,,,,,,, Andy
- Zomerset Zed
- 100Club
- Posts: 129
- Joined: 30th May 2014
- Location: Somerset
- Zomerset Zed
- 100Club
- Posts: 129
- Joined: 30th May 2014
- Location: Somerset
Long overdue update
I thought it was about time i made a long overdue update:
Excuses: work, not being in the country, shite weather new bike etc. blah, blah
What have i done?
Clutch basket stripped, blasted new APE repair kit installed. I did do a full photo step by step instructions for this but i have lost on old phone. But it was fun and all done "in-house":
Holes have to be drilled out precisely as pins are larger diameter and then spacer collars heated with blow torch and hammered like fuck onto the pins. Then all needs to be clamped up and ends of pins welded up.
Next up - More frame mods
Excuses: work, not being in the country, shite weather new bike etc. blah, blah

What have i done?
Clutch basket stripped, blasted new APE repair kit installed. I did do a full photo step by step instructions for this but i have lost on old phone. But it was fun and all done "in-house":
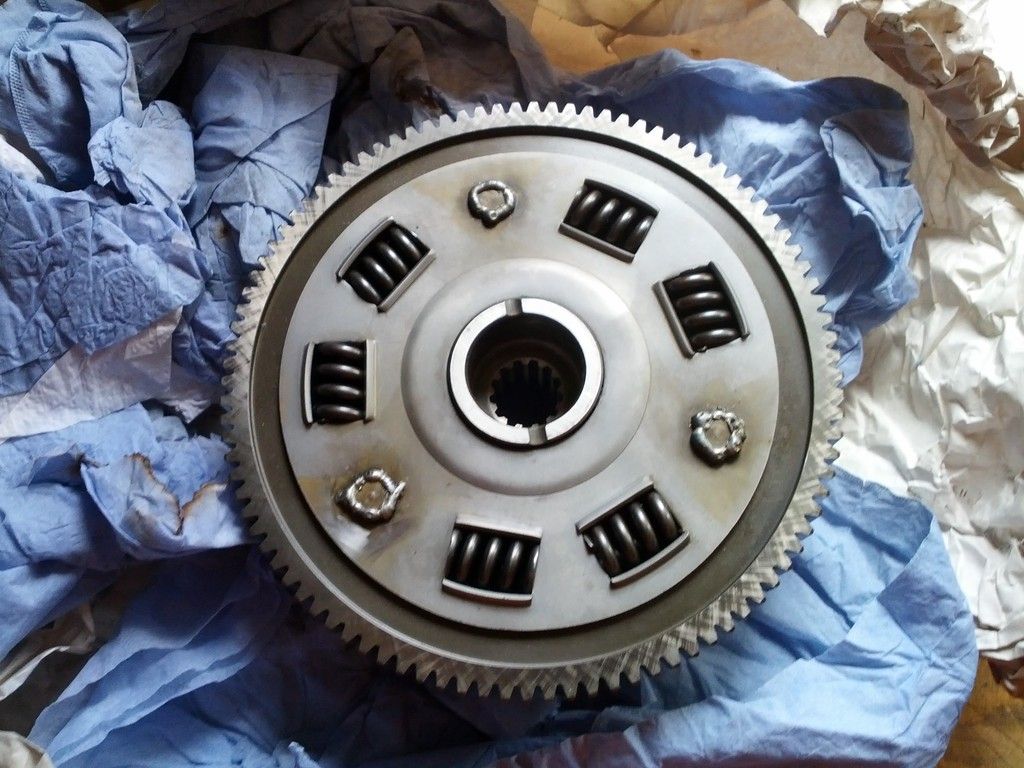
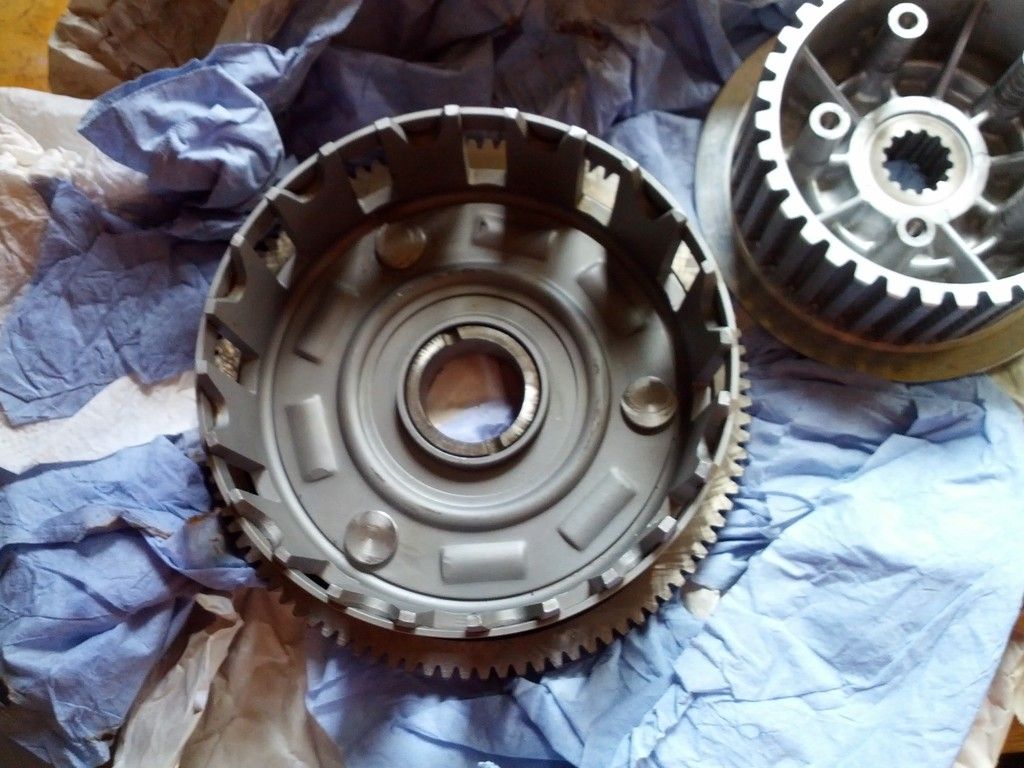
Holes have to be drilled out precisely as pins are larger diameter and then spacer collars heated with blow torch and hammered like fuck onto the pins. Then all needs to be clamped up and ends of pins welded up.
Next up - More frame mods

- Zomerset Zed
- 100Club
- Posts: 129
- Joined: 30th May 2014
- Location: Somerset
Frame mods
Again i lost all of the step by step photos, so here are the nearly complete results:
Tube bracing to reduce head-stock twist
Secondary plate welded in to create a box to reduce head-stock twist
Plating to undo someones previous "enhancements"
Rear horizontal members now welded in to reduce twisting of the cradle at the rear
Upper and lower chain run "channels" created to allow fitment of 6" rear wheel. Note how i have cunningly incorporated a frame brace into the deal. Something which Sanctuary do not do. Tacked into position awaiting parts to be made to complete the chain run and rear wheel placement.
RHS bracing to strengthen up rear "sub-frame"
Cut up sprocket cover (it was split anyway) to get chain run in.
No expense spared high tech drilling jig for new top shock mounts
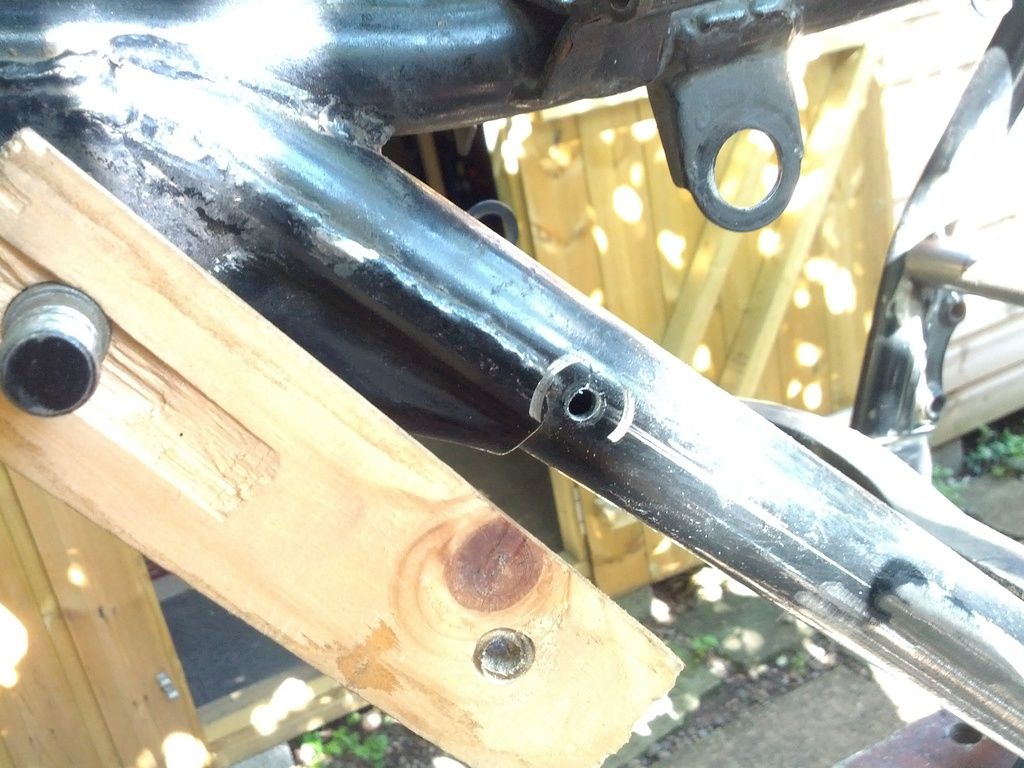
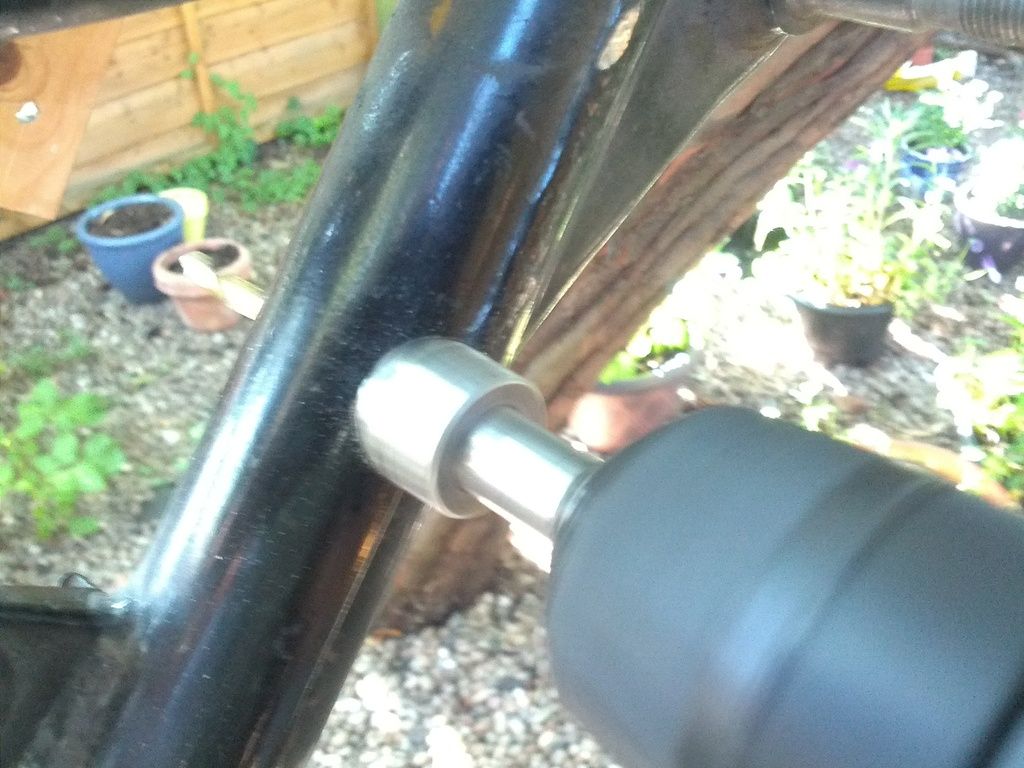
Now waiting for top shock mount so i can position in frame and weld in place
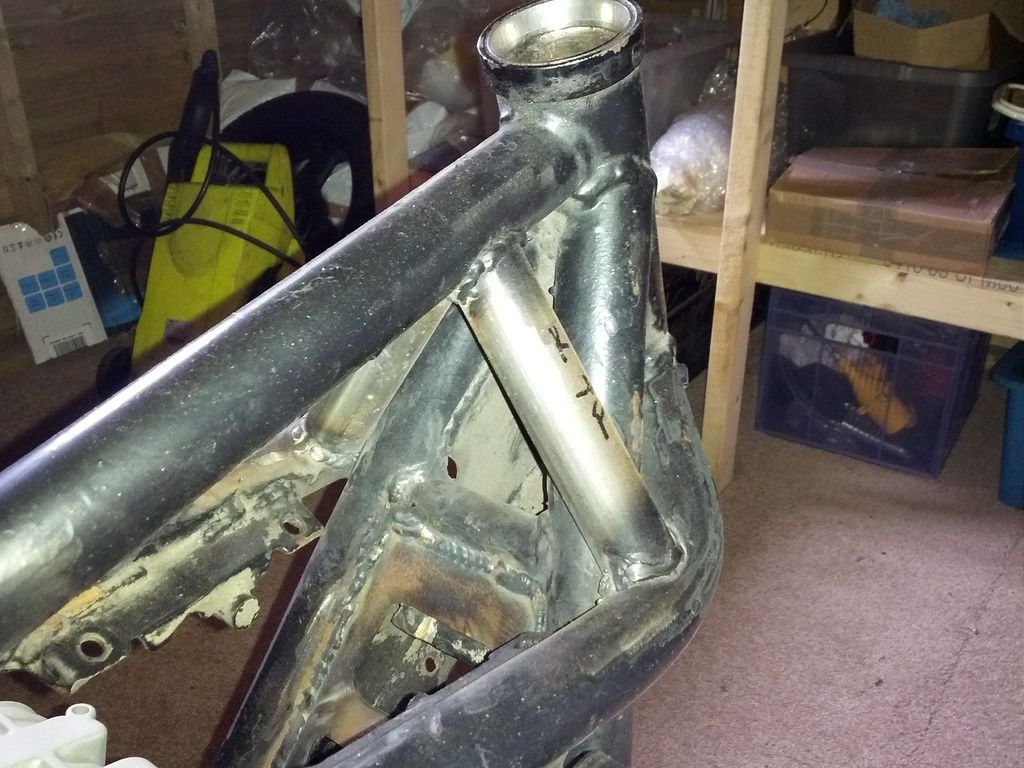
Tube bracing to reduce head-stock twist
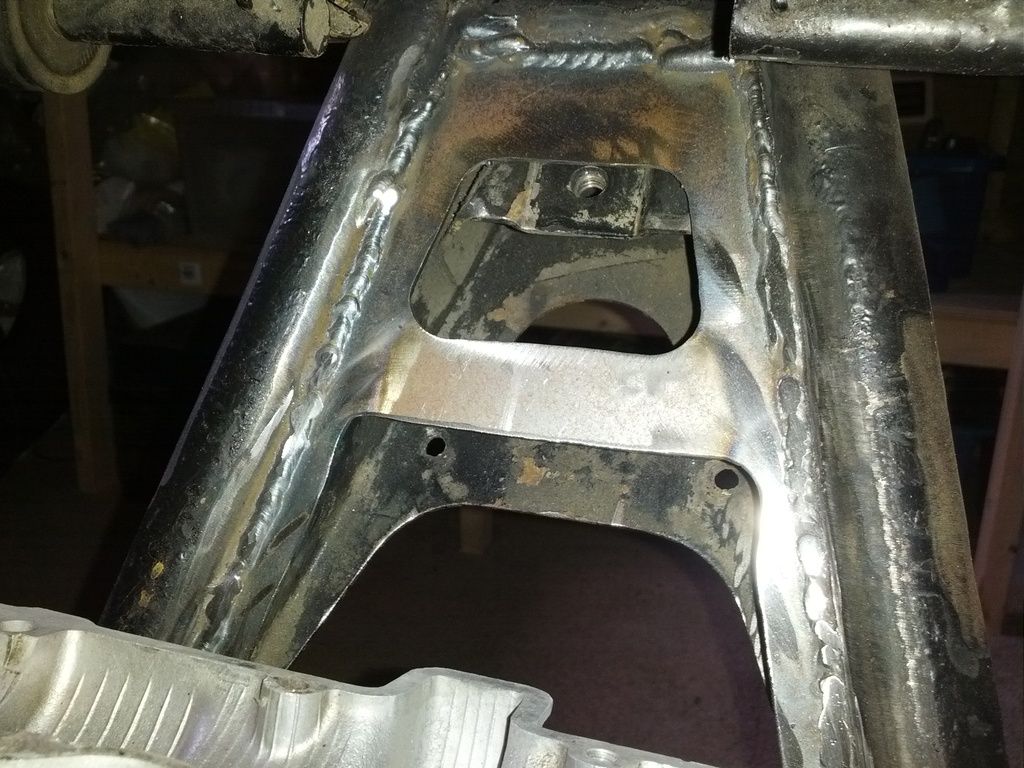
Secondary plate welded in to create a box to reduce head-stock twist
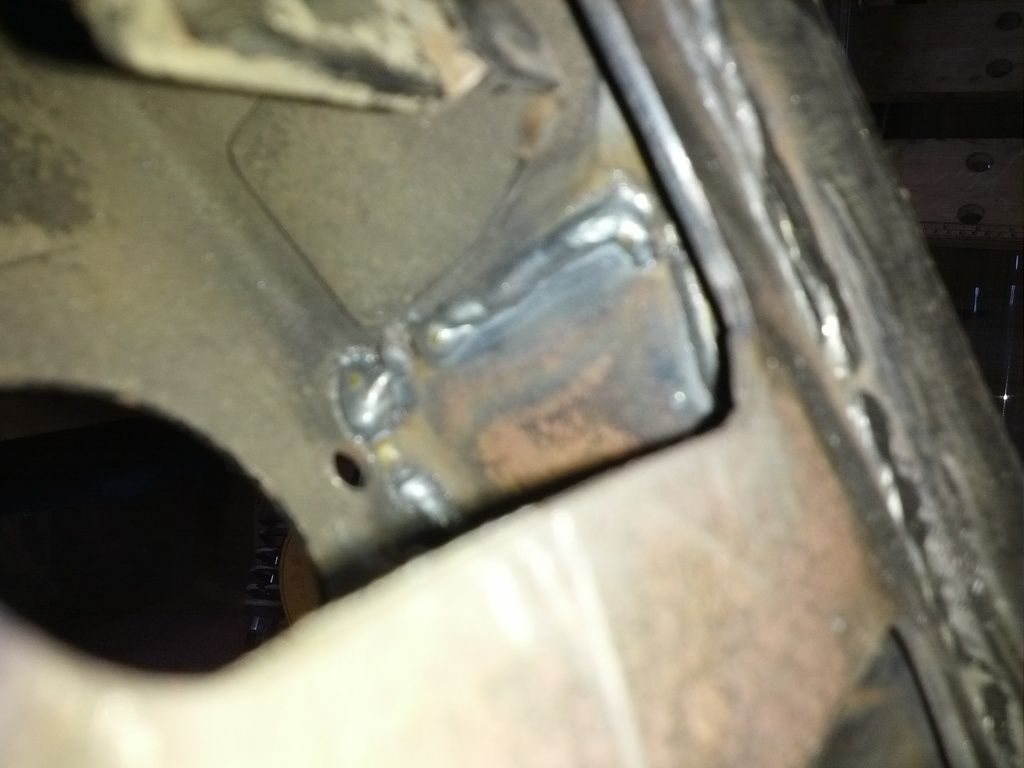
Plating to undo someones previous "enhancements"
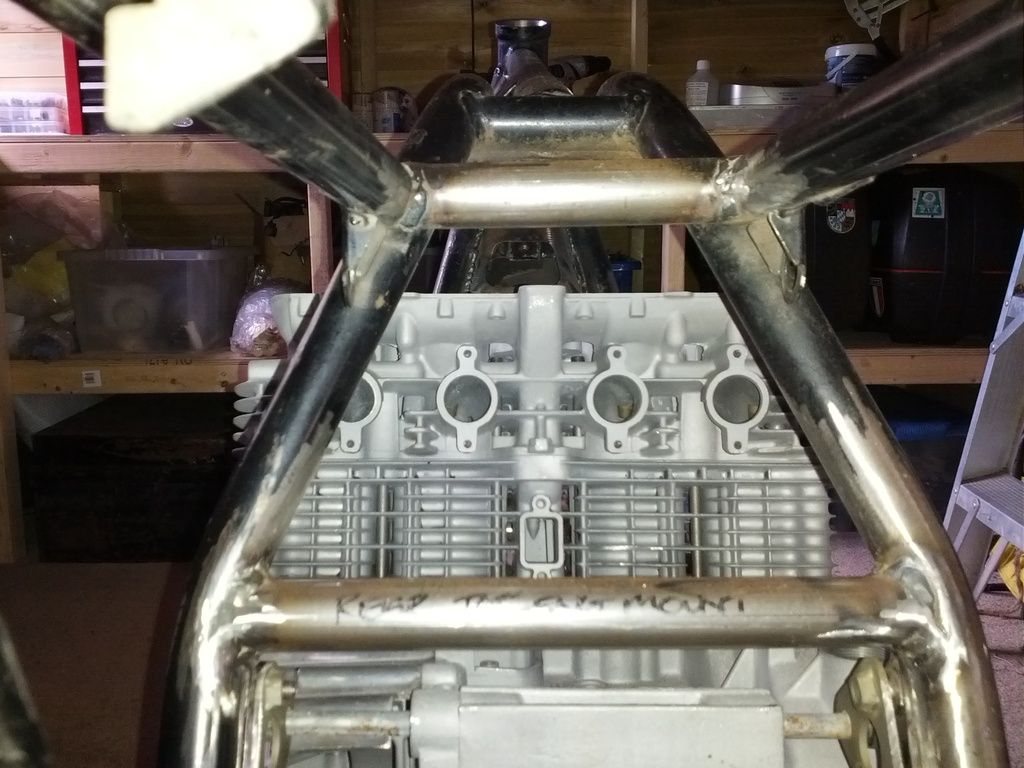
Rear horizontal members now welded in to reduce twisting of the cradle at the rear
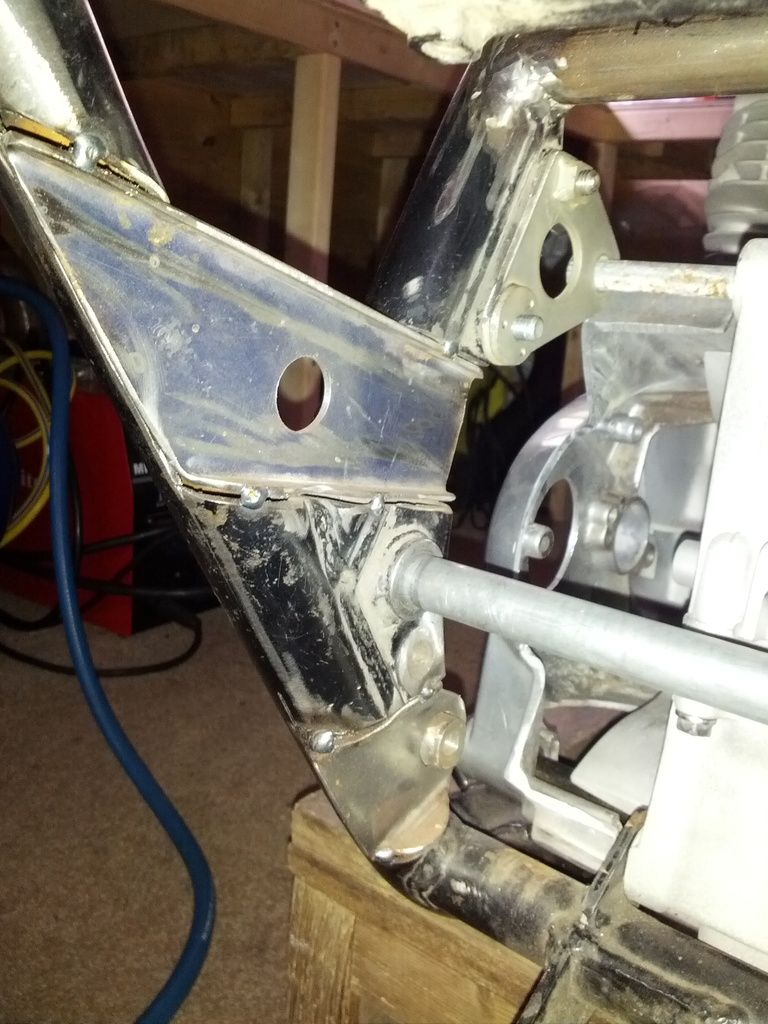
Upper and lower chain run "channels" created to allow fitment of 6" rear wheel. Note how i have cunningly incorporated a frame brace into the deal. Something which Sanctuary do not do. Tacked into position awaiting parts to be made to complete the chain run and rear wheel placement.
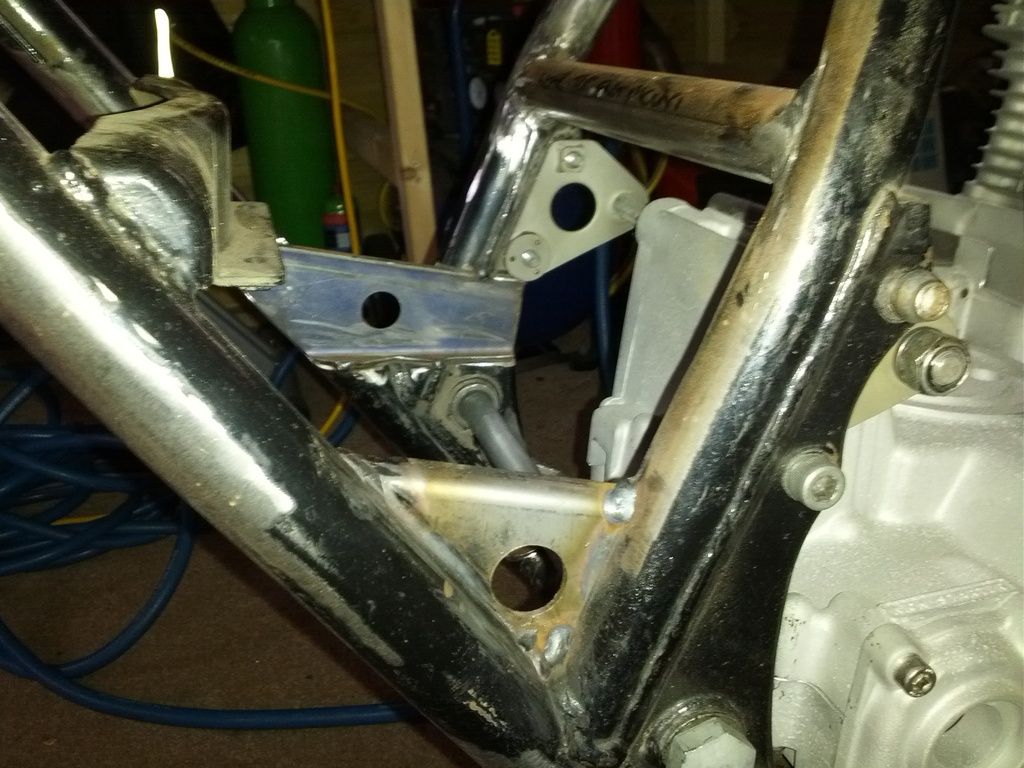
RHS bracing to strengthen up rear "sub-frame"
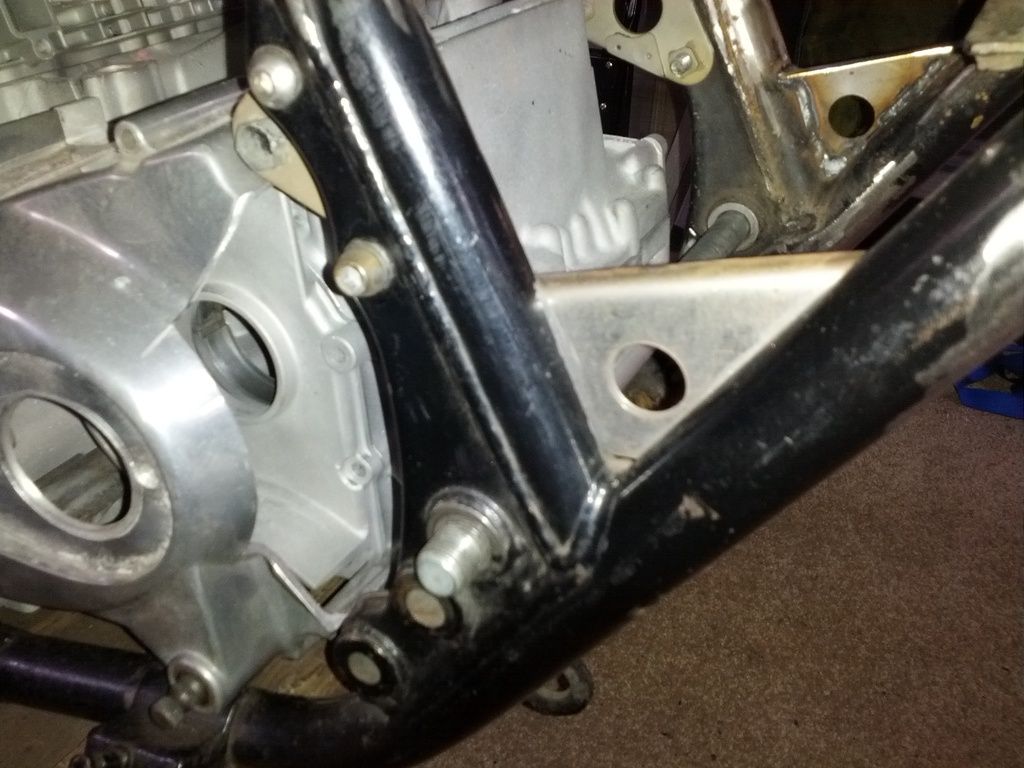
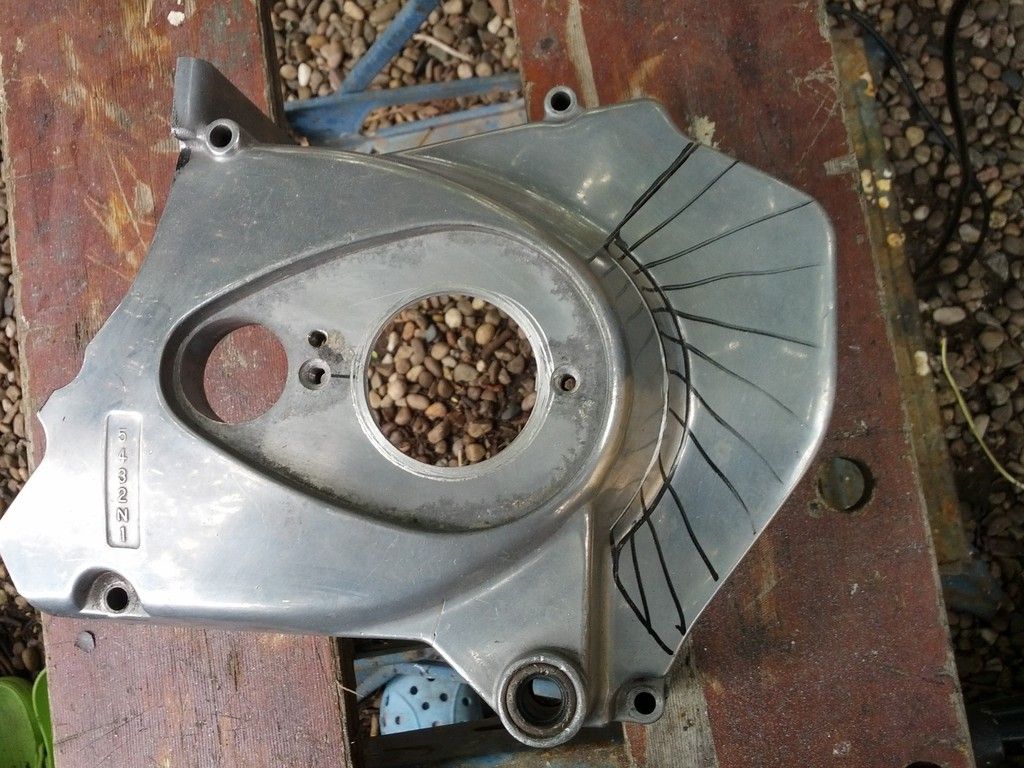
Cut up sprocket cover (it was split anyway) to get chain run in.
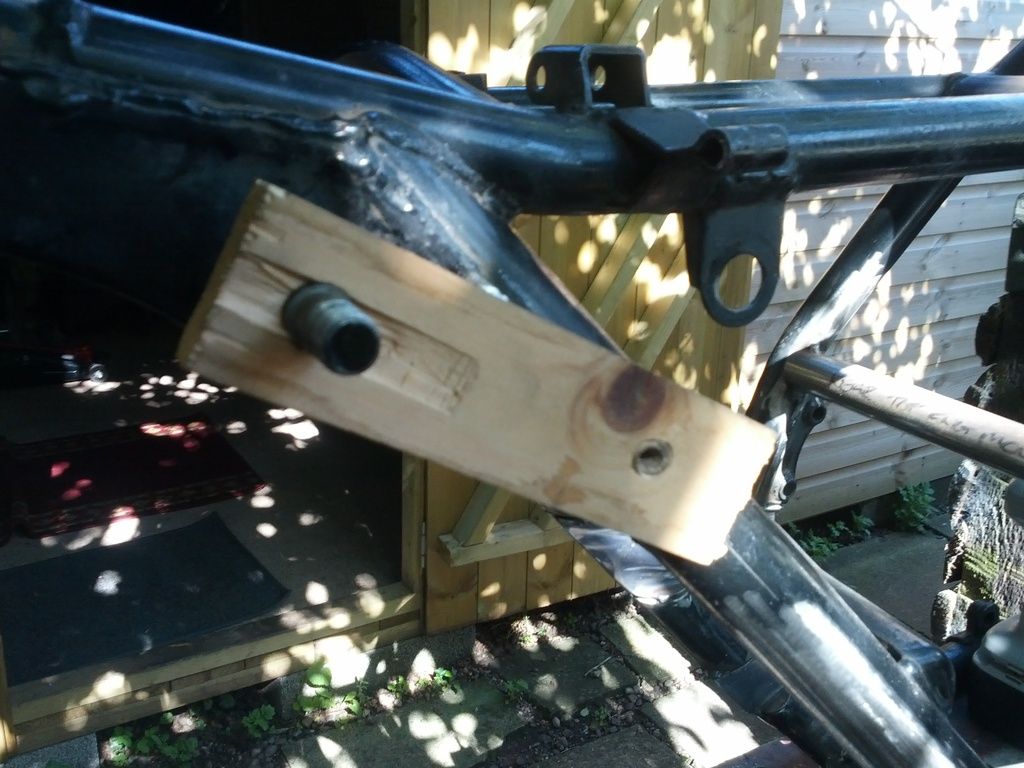
No expense spared high tech drilling jig for new top shock mounts
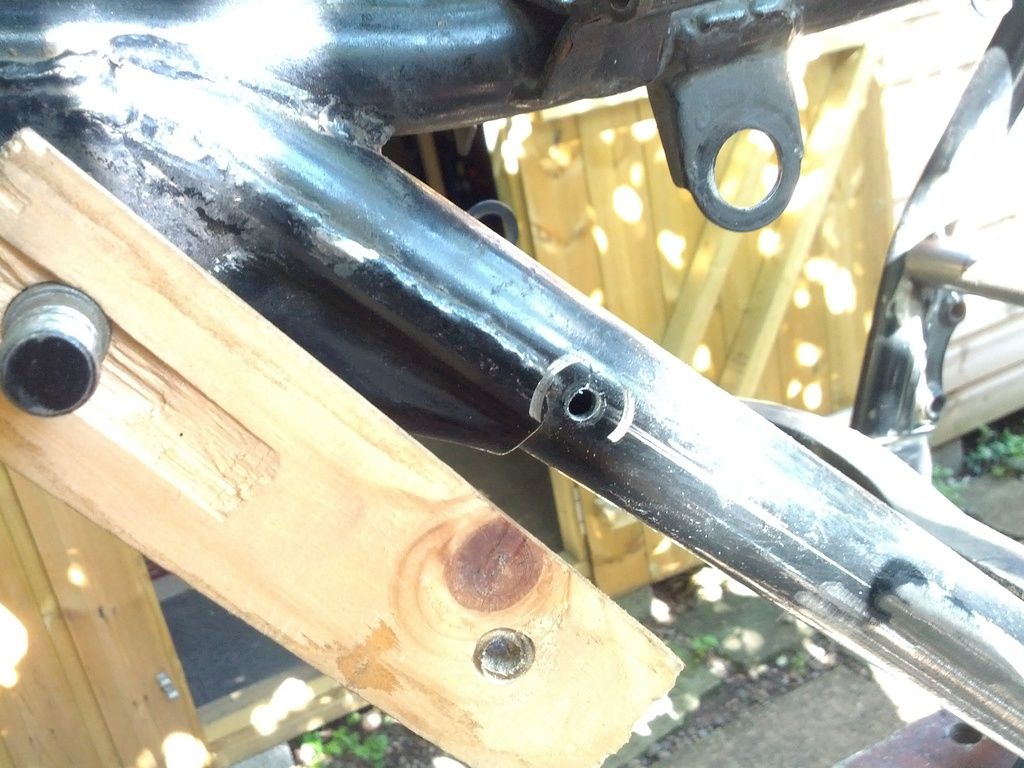
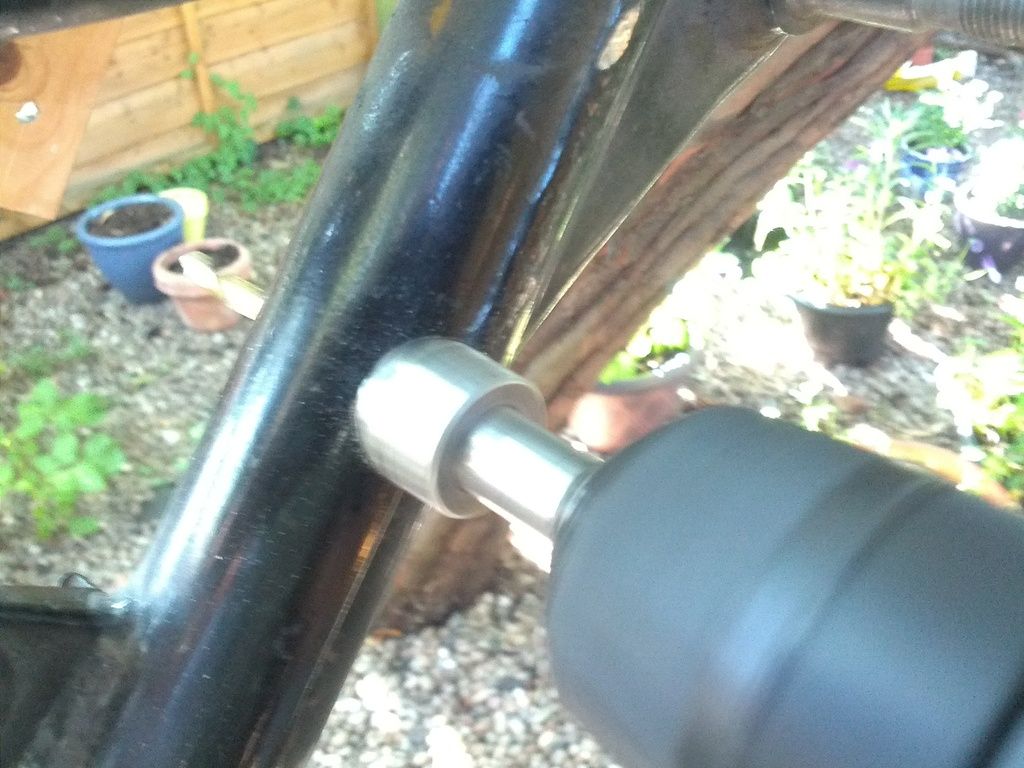
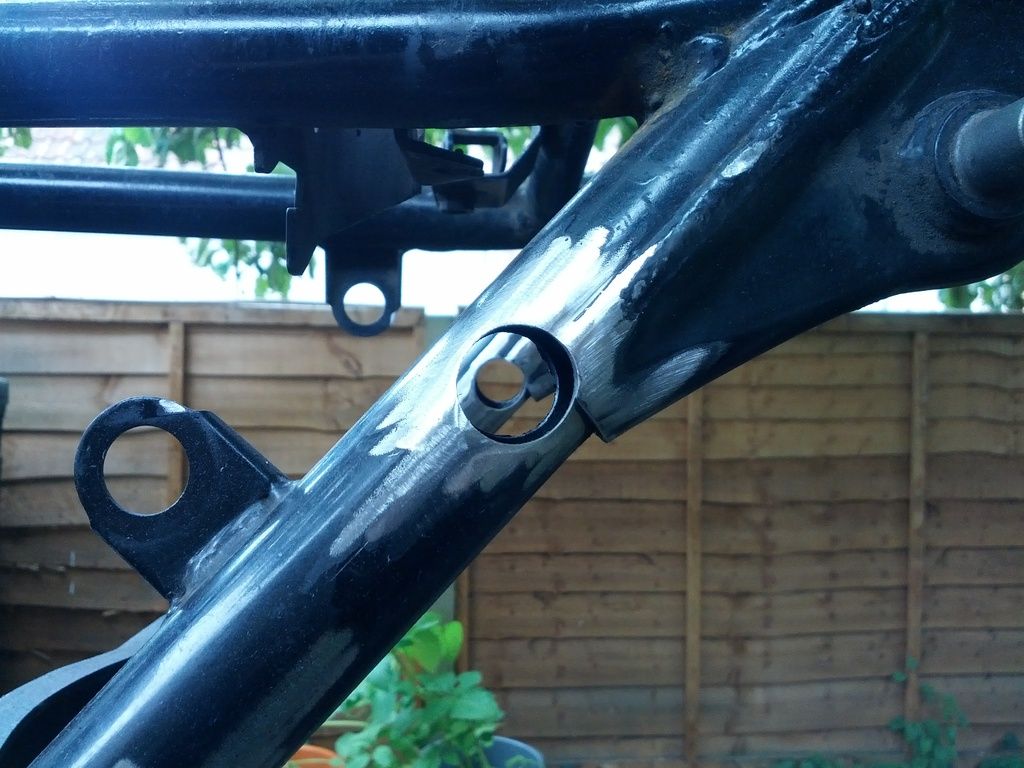
Now waiting for top shock mount so i can position in frame and weld in place
- Zomerset Zed
- 100Club
- Posts: 129
- Joined: 30th May 2014
- Location: Somerset
- Ginger Bear
- Hardcore
- Posts: 6850
- Joined: 16th Dec 2008
- Location: In the Dark.
- Contact:
- Zomerset Zed
- 100Club
- Posts: 129
- Joined: 30th May 2014
- Location: Somerset
Yokes
This is what i am doing to mount the R6 forks:
Top yoke, bar clamps, new stem and other bits and bobs are being CNC machined at the moment. I am using the standard R6 bottom yoke.
I have procured an R6 front wheel and monoblock radial calipers, so once i get the machined parts back i can build up a complete front end. Just need to find some discs i like at a reasonable price.
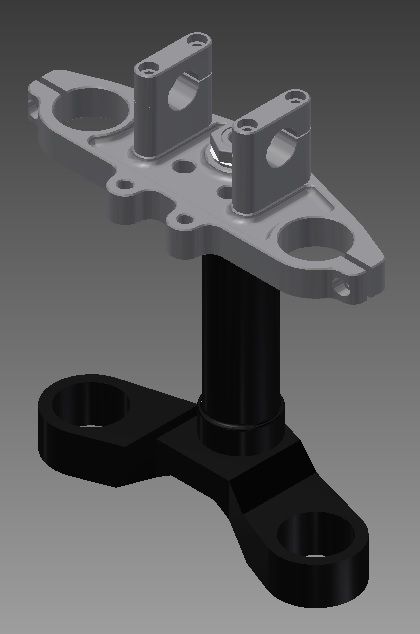
Top yoke, bar clamps, new stem and other bits and bobs are being CNC machined at the moment. I am using the standard R6 bottom yoke.
I have procured an R6 front wheel and monoblock radial calipers, so once i get the machined parts back i can build up a complete front end. Just need to find some discs i like at a reasonable price.
- Zomerset Zed
- 100Club
- Posts: 129
- Joined: 30th May 2014
- Location: Somerset
Outrigger bearing
This is what i am doing to support the longer output shaft:
I am mounting a ball bearing inside the sprocket on a new +25mm output shaft which will have an R1 spline cut into it rather than the Z1000 spline to mount the sprocket on. This will allow me to run standard R1 sprockets front and back in either 520 or 530. It will allow me to get the chain alignment spot on in practice by adjusting the length of the spacer between the sprocket and the gearbox bearing. When/if i want to change the gearing or when the sprocket wears, i just buy a new standard R1 sprocket. I am also fitting a case saver and one of Falk Stumms hydraulic cylinders.
All this also fits under the standard housing, so externally looks like a bought one
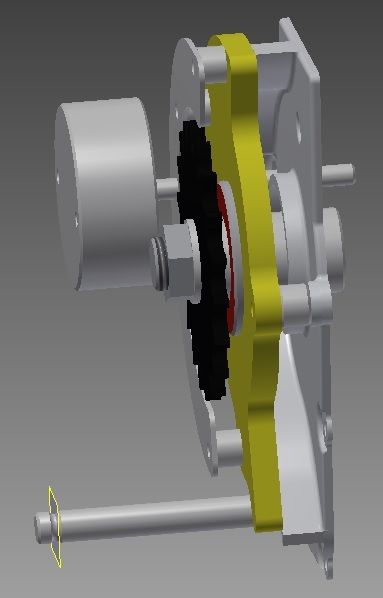
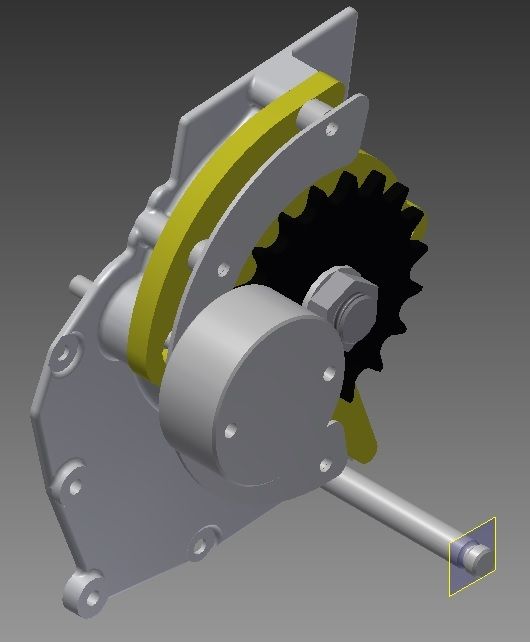
I am mounting a ball bearing inside the sprocket on a new +25mm output shaft which will have an R1 spline cut into it rather than the Z1000 spline to mount the sprocket on. This will allow me to run standard R1 sprockets front and back in either 520 or 530. It will allow me to get the chain alignment spot on in practice by adjusting the length of the spacer between the sprocket and the gearbox bearing. When/if i want to change the gearing or when the sprocket wears, i just buy a new standard R1 sprocket. I am also fitting a case saver and one of Falk Stumms hydraulic cylinders.
All this also fits under the standard housing, so externally looks like a bought one

- Zomerset Zed
- 100Club
- Posts: 129
- Joined: 30th May 2014
- Location: Somerset
- Zomerset Zed
- 100Club
- Posts: 129
- Joined: 30th May 2014
- Location: Somerset
Who is online
Users browsing this forum: No registered users and 5 guests